Customer reference: WOLF GmbH – 25 years of Kanban
With 9 subsidiaries and 60 sales partners worldwide, WOLF is an expert in the field of heating and ventilation in Mainburg, and at the same time has international presence. In addition to Germany, WOLF has subsidiaries and partner companies in more than 50 countries. The company supports planners, installers and end customers in holistically planning and coordinating energy-efficient heating and ventilation solutions. To put it in a nutshell: the products of the WOLF Group provide an optimal indoor climate all over the world – from single and multi-family houses to office buildings, airports and railway stations, hotels and government buildings, football stadiums and leisure parks, hospitals and baths, and industrial environment.
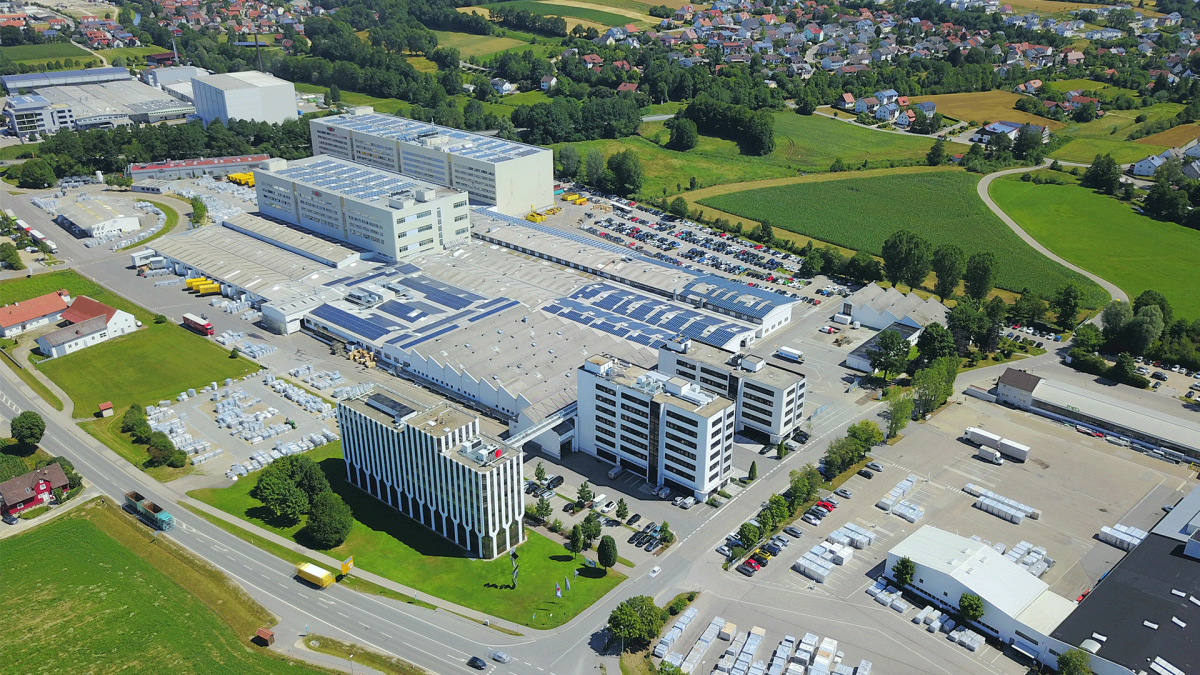
Modern, sustainable C-Parts management means far more than just supplying the required items. In fact, the supplier is now developing into a comprehensive partner who is integrated into the system-based process landscape, and uses holistic, automated systems and services that reduce process costs while increasing productivity, quality and flexibility. Even though C-Parts represent a small proportion of the purchase volume of the company, the procurement efforts involved are high. This is exactly where the supply solutions for the automated production supply of Würth Industrie Service at WOLF have come into picture since 1997.
Objective of the production supply
- Supply security through automated re-ordering
- 24-hour availability
- Innovative technologies
- Complete transparency of all processes, withdrawals and orders
- Safe and needs-based storage
The solution: The highly flexible Kanban systems
For more than 25 years, the heating and ventilation specialist WOLF has relied on the innovative system portfolio of the C-Parts expert, and is one of the first Kanban customers to rely on highly flexible RFID supply systems to optimise production processes within the assembly. A look into the past indicates the development at WOLF: Starting with simple, labelled bins that were manually provided by a system administrator of Würth Industrie Service for refilling for return transport, WOLF initially opted for conventional Kanban processing. A hand scanner was used to trigger demand. At the beginning of 2017, the RFID transition took place at the Mainburg site. Since then, the reordering process has been completely automated and demand-oriented, for example, using the intelligent shelves iSHELF®. If a bin is empty, then the integrated shelves directly detect it via an integrated sender-receiver-unit in the shelf. The shelf reads the RFID chip and transfers the information about the empty bin directly to the Kanban-Management-System (KMS) of Würth Industrie Service developed in-house. The supply takes place centrally from the European logistics centre in Bad Mergentheim to WOLF. Other RFID-based system solutions are also used. For example, the intelligent pallet box iBOX®, which immediately transmits the data via RFID as soon as an empty bin is placed in there. The rest is handled altogether autonomously by the system. The demand is transmitted transparently and securely to the ERP system of Würth Industrie Service, and the subsequent delivery of the required items is triggered automatically. In addition, iPUSH® is used for easily transmitting the demand by pressing a button. With iPUSH®, the order is triggered by pressing the button integrated into the RFID module. In more than 40 Kanban storage locations spread over four floors, a total of around 2,200 active bins are equipped with various items, which are used in the assembly of the heating and ventilation solutions at WOLF. The portfolio comprises over 400 different items, ranging from screws, nuts and rivets to sealing bands, drawing parts and small electrical parts. A system administrator of Würth Industrie Service refills them at weekly intervals.
The result: Maximum supply security through highly flexible Kanban systems
“Through RFID-Kanban, we benefit from increased productivity and additional time and cost savings across all areas: Our assembly needs are managed in a lean manner and reordered automatically - without manual intervention.” Ernst Kranert, Head of Purchasing at WOLF.
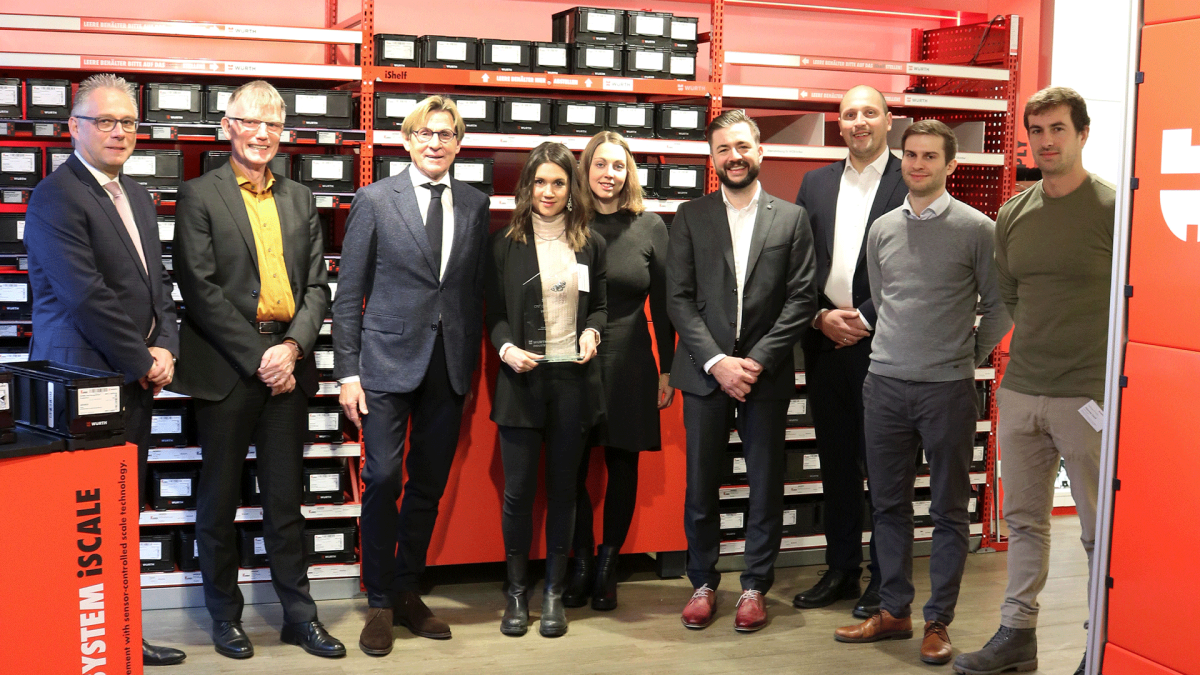
An occasion to celebrate: 25 years of Kanban
On 15th and 16th December 2022, WOLF and Würth Industrie Service celebrated 25 years of Kanban in Bad Mergentheim. An evening event was held to look back on the past cooperation and to talk about future projects. Thomas Schmid, Account Manager at Würth Industrie Service, who has been in charge of WOLF for over eight years, remembers: “Exactly 25 years ago, the first Kanban bins were delivered to Mainburg – from our then location as Industry division of our parent company in Gaisbach. Since then, around 106,000 bins have been in circulation with about 1,000 refills.” As a notable innovation pioneer, WOLF is considered one of the longest-standing customers. “It is therefore a matter of course for us to duly acknowledge the loyalty of our customers.” said Mr. Schmid.
Further success stories of our supply systems
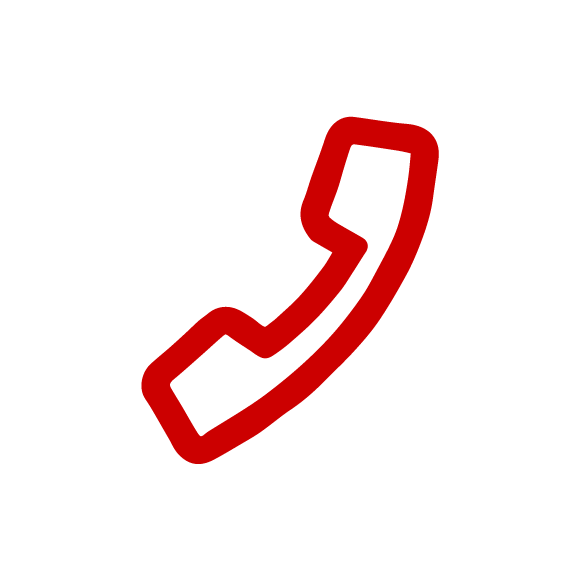
Contact
We are there for you!
Contact us at T +49 7931 91-0 or by e-mail at cps@wuerth-industrie.com.
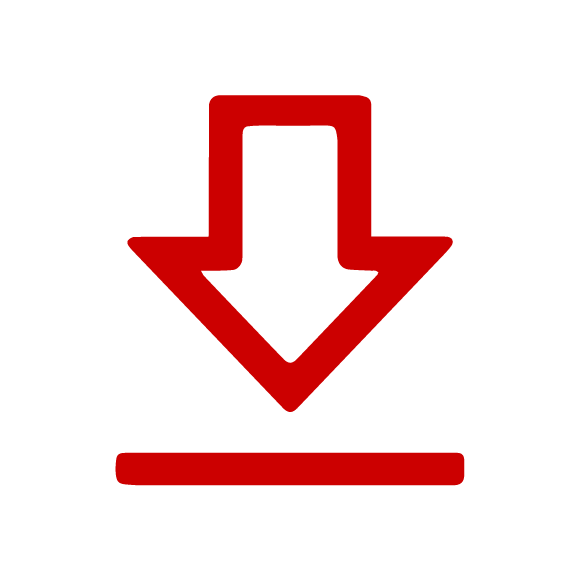
The Würth Industrie Service GmbH & Co. KG collects and processes the personal data provided in the form in order to process the requested request for you. Please note the mandatory fields in the forms. The legal basis for this processing, the absolutely necessary data, is Art. 6 para. 1 lit. b DSGVO, implementation of a pre-contractual measure. The processing of data voluntarily provided by you is carried out on the basis of Art. 6 para. 1 lit. f DSGVO. Thereafter, processing is permissible which is necessary to safeguard our legitimate interests. Our legitimate interest is to have contact with you, our customers, to improve our consulting quality and to be able to contact you more easily in case of possible queries. The data collected will only be stored by us for as long as is necessary to process your enquiry and to contact you. They are then deleted.
Supplementary data protection information, in particular regarding your rights to information, correction, deletion, restriction of processing, objection and complaint, can be found in our data protection declaration.